Статьи
Сообщить о проблеме
«Для нас было важно полностью закрыть всю линейку морских лакокрасочных покрытий одной маркой»
"Русские краски" расширяют перечень продукции для судостроения и судоремонта, прошедшей испытания в сертификационных органах. С начала 2024 года компания получила четыре свидетельства о типовом одобрении Российского морского регистра судоходства (РС) на продукцию линейки РК-Marine. О новых продуктах, об особенностях лакокрасочных материалов (ЛКМ) для различных типов судов, о текущей ситуации на рынке, а также о возникших в последнее время проблемах и путях их решения в интервью Sudostroenie.info рассказал директор бизнес-направления "Авиация и судостроение" АО "Русские краски" Александр Гареев.
– Александр Олегович, какие новые ЛКМ для морской индустрии сегодня разрабатывают "Русские краски"?
– Работы по новым материалам наша компания ведет постоянно. На рынке судостроения и судоремонта мы присутствуем уже почти 8 лет и практически каждый год выпускаем новые морские лакокрасочные покрытия. Сейчас мы проводим полную сертификацию материалов с новыми эпоксидами, будем выводить новое ледовое покрытие первого класса уровня ведущих зарубежных производителей, разработали и готовим к выводу на рынок новый грунт, адаптированный для удобства пользователей.
Еще один интересный и сложный продукт, который в настоящее время проходит сертификацию, – покрытие для топливных цистерн. Материалов такого уровня раньше в России не было. До этого использовались только классические материалы 1970-х годов разработки. Сложность такого материала заключается в минимизации воздействия на топливо, которое хранится в цистерне. Разработка такого материала – достаточно сложный процесс с очень дорогостоящими испытаниями.
Кроме того, недавно сертифицировали покрытие для питьевых цистерн. Это не менее сложный продукт. В "питьевке" мы должны одновременно соединить гигиенические нормы, которые подразумевают отсутствие вреда для здоровья людей, и очень жесткие требования по антикоррозионной защите. Это прямо противоречащие друг другу показатели, мы их «скручивали» года три. Это была сложная работа, но мы ее провели. В итоге материал сделан и прошел всю сертификацию.
Потребность в таких материалах появилась после ухода с рынка иностранцев. Несмотря на то, что объем рынка таких покрытий очень маленький, спрос на них есть. Наша цель – полностью окрасить судно или корабль, для этого нам надо закрывать и эти вопросы.
Сложность здесь заключается в том, что все поверхности находятся в разных климатических и антикоррозионных условиях, подвергаются разным воздействиям: топливо, вода, лед, обрастания, атмосфера, солнце, кислоты. Это очень разные условия эксплуатации. Поэтому для нас было важно полностью закрыть всю линейку морских лакокрасочных покрытий одной маркой.
– Это удалось?
– По факту, уже да. Вся линейка лакокрасочных покрытий закончена, осталось завершить некоторые сертификационные процедуры.
– В ходе нашего общения в прошлом году вы оценивали долю рынка компании примерно в 10%. Ситуация изменилась?
– Практически нет. Новая сложность в том, что мы не всегда понимаем, что с рынком сейчас происходит по факту. Объективных данных, от которых можно было бы оттолкнуться, нет. Если до 2022 года все данные были открыты, все производители известны, а все объемы понятны и прозрачны, то после после ухода иностранцев мы не можем точно просчитать, что с рынком происходит. По нашим ощущениям, он сократился, объемы строительства притормаживаются.
В то же время рынок очень инерционный и останавливается медленно. Если проект запущен, то его пытаются довести до конца. Но сдачи точно сдерживаются, потому что у нас есть примеры верфей, которые практически всё достроили, спустили на воду, но при этом сдать не могут из-за того, что отсутствует несколько агрегатов, которые не могут быть поставлены по понятным причинам. Верфи не могут получить деньги, соответственно, не могут получить новые проекты. Эта ситуация точно есть, но в каком масштабе, у нас нет точных данных.
Среди других факторов – практически неконтролируемый приход на рынок множества небольших производителей. Мы не очень понимаем, что с китайцами, которые заходят на наш рынок, какую долю они забирают. Не видим, сколько завозится параллельным импортом, потому что это закрытые схемы, которые не отражаются в отчетности.
Плюс реформирование и реорганизация в ряде корпораций ведет к тому, что некоторые проекты приостанавливаются. Это тоже сказывается на рынке. Поэтому мы свою долю так же примерно оцениваем в 10%, но мы стали хуже чувствовать цифры.
– Поговорим о специфике продукции для разных сегментов. В последние годы набирают популярность электросуда. У "Русских красок" есть продукция для таких судов?
– Да. Например, наша продукция используется на верфи электрического судостроения "Эмпериум", куда мы поставляем шпаклевку. Недавно в Ярославле был спущен на воду полностью нами покрашенный электрокатамаран "Белояр", построенный на верфи "Паритет-Центр".
Особенность электросудов в том, что там используется алюминий, а у нас есть яхтенная линейка, созданная с учетом опыта работы с авиацией. Когда мы начинали на судостроительном рынке, у нас был большой плюс – авиационные материалы, и мы могли использовать этот опыт. Там же тоже используется алюминий, поэтому мы смогли создать линейку яхтенных материалов, которой нет у других российских производителей. По сравнению с морскими яхтенные покрытия имеют совсем другой вид, там другой глянец.
Эту линейку как раз использовала верфь "Паритет" для окраски катеров проекта "Лукер" и небольших яхт, а затем и для большого электрокатамарана. Поэтому с учетом того, что у нас есть опыт работы с яхтенной краской и алюминием, для нас переход на "электрички" не создает никаких проблем. Мы спокойно можем это делать.
– В чем особенность яхтенного сегмента?
– Здесь меньше борьбы с коррозией, важнее внешний вид. Эти покрытия ближе к авиационным покрытиям, где очень высокие требования. Ведь самолеты под солнцем находятся большую часть времени, а влияние ультрафиолета в воздухе намного жестче, чем у любого объекта на земле. Плюс еще жесткость в перепадах температуры. Если у нас погода меняется плюс-минус пять градусов в течение дня и постепенно, то здесь перепад от минус 40 до плюс 40 градусов происходит в течение часа. Для краски это очень серьезная нагрузка.
Имея в руках разработанные материалы для авиационной отрасли, нам легко было перейти и сделать материалы для яхтенного сегмента.
– В последние годы также развивается композитное судостроение. С композитами вы работаете?
– На композиты материалы идут те же самые материалы, только толщина грунтовок другая. В данном случае материалы несут больше связывающую функцию между эмалью и самим композитом. Если в стальном судостроении идет в основном антикоррозионная работа, то здесь опять же ближе к декоративным материалам.
– А что касается ЛКМ для грузовых судов, например, сухогрузов?
– С ними проще. Все основные материалы уже давно разработаны. Сейчас мы просто их продолжаем улучшать.
– Вы упомянули разрабатываемый материал для ледокольного флота. С этим сегментом вы уже работаете?
– Мы начали работать, но сейчас стоит большой вопрос, что делать дальше с ледокольным флотом. Нам неожиданно предъявили требования, что все заказчики хотят первый класс, но вопрос в цене. Ледокольное покрытие уровня Inerta 160 или Marathon IQ в Европе и Китае стоит около 3 тыс. рублей за литр. В России подобные покрытия некоторые производители предлагают за 1,5 тыс. рублей. Мы в некотором недоумении по этому поводу, потому что все знают, сколько стоят компоненты для таких покрытий. Например, там используются исключительно отвердители от одного конкретного западного производителя сырья.
Часто задают вопрос, почему для лакокрасочных материалов используются импортные компоненты, ведь в основе – та же нефть. Проблема в том, что между нами и "нефтянкой" стоит целая отрасль – химическая. Мы стоим четвертым-пятым уровнем и не можем взять продукты нефтепереработки и из них сделать краску. Нам еще нужна целая отрасль, на которую никто не обращал внимание, и она практически полностью в России теперь отсутствует. Поэтому большая часть химии – импорт.
В целом лакокрасочная отрасль очень глобальна. В мире нет страны, в которой от "нефтянки" до краски все делается внутри. Поэтому цены глобальные, все их прекрасно знают. Плюс-минус 10-20% играют, но вариант, что материал, который стоит три тысячи, а продается за полторы, для нас пока остается загадкой.
Мы со своей стороны делаем покрытие уровня Inerta. Мы понимаем, что оно будет точно немного дешевле, чем европейские аналоги, но на их уровне. Дальше будем действовать исходя из того, что рынок захочет. Если рынок продолжит брать дешевые материалы и делать ставку на цену, значит будет материал, который хочет рынок. Только потом будет обидно, когда начнут говорить, как это было раньше, что в России производят не очень хорошее качество, а вот у европейцев было "совсем другое".
– Сколько по времени занимает разработка новых материалов?
– В среднем на разработку одного материала в нашем научно-исследовательском центре уходит от одного года до трех лет. Далее встает вопрос сертификации. После того, как мы проходим собственные внутренние испытания, у нас еще есть испытания для ВМФ и гражданских заказчиков. Там испытания длятся до полутора лет. Если все хорошо, то полный цикл занимает до 4-5 лет. Если мы говорим о серьезных материалах, то это примерно такие сроки. Соответственно, и глубина планирования для таких ЛКМ у нас должна быть достаточно длинной.
Есть, конечно, покрытия, которые делаются быстрее. Как раз так получается с подводным бортом.
– На какой срок службы рассчитаны материалы "Русских красок"?
– В последнее время для некоторых материалов мы продлили срок службы до 15 лет, даже для подводного грунта. До этого мы все испытания проводили на срок до 5 лет. Увеличение в 3 раза связано с высокими требованиями государственных заказчиков к морским покрытиям. Этот же грунт используем и на гражданские суда, поэтому там сроки службы тоже увеличились.
Хотя это отдельная большая тема – сроки службы, которые нужны клиенту. Мы на протяжении всего времени работы смотрели на международные компании. Российский рынок морских покрытий, в отличие от индустриального рынка, на 80% занимали иностранцы. Этот рынок был не элитным, но с точки зрения качества материалов очень высоким. Когда мы заходили на рынок, к нам были требования выпускать материалы не ниже мировых стандартов. Мы на это изначально были нацелены. И завод может себе это позволить, и научно-исследовательский центр у нас очень большой. В результате мы довели уровень материалов до мирового, а по некоторым позициям даже выше, чем у иностранцев.
Но после ухода иностранцев рынок поменялся, в моем понимании, в худшую сторону. У нас сейчас в этом году первым и главным показателем на 90% стала цена. В целом рынок стал очень резко падать по качеству. Стали заходить неспециализированные производители, которые думали, что иностранцы ушли, соответственно, место освободилось. С индустриального рынка стало много компаний заходить. Интересно, что на мировом рынке происходит наоборот: там изначально создаются продукты для сложного рынка морских покрытий, затем эти продукты упрощаются до индустриального рынка, а далее – до рынка декоративных материалов. В России мы зачастую наблюдаем противоположную тенденцию.
В результате этих процессов стали резко падать требования к материалам. И это на самом деле колоссальная проблема, потому что для нас это некоторое переформатирование. Мы, конечно, перестроимся, но в целом то, что требования к материалам снизились, это очень печально.
– Кто снижает требования, заказчик судна?
– Зачастую, да. При этом сам же заказчик часто жалуется, что он хотел бы получать материалы все того же уровня, но вынужден в связи с законодательством и, иногда, в связи с формальным подходом некоторых подразделений, выбирать исключительно по цене.
В итоге заказчик получает материалы, которые служат 2-3 года – срок гарантии. Что с ними будет потом происходить, никто не представляет, да и никто сильно не беспокоится по этому поводу. Это на самом деле огромная проблема для всех производителей, которые работают на этом рынке. Последние лет пять мы все занимались качеством. Мы разгоняли материалы до уровня мировых производителей, но происходящее сейчас всю эту систему рушит.
– Как приоритет цены при закупках сочетается с разработкой перспективных материалов?
– Это очень плохо для науки, которая занималась разработкой этих материалов. В целом качество отечественных материалов начинает падать. С такой ситуацией мы вернемся к тому, что было лет 15 назад.
Что с этим делать, никто пока не знает. Единственный вариант, который у нас есть – выпускать разные линейки. Для тех клиентов, которым важна долговечность антикоррозионных материалов, мы делаем одну линейку. Для тех, кто просто смотрит на цену, делается вторая линейка.
– Что могло бы изменить эту ситуацию?
– Вопрос к заказчикам, чего они хотят. Что важнее, влезть в бюджет, и чтобы те подразделения, которые отвечают за закупки, получили KPI за снижение цены, или получить материалы высокого уровня. Большинство заказчиков выбирают вариант попроще, подешевле, глубоко не вникая. Специалистов, которые в этой теме понимают, становится все меньше и меньше.
В крупных корпорациях еще есть такая проблема. У них нет человека, который будет с кораблем работать 5-10 лет, там происходит постоянная ротация через 1-3 года. Соответственно, у них нет длинной ответственности. В итоге, если все это будет продолжаться, мы получим то, что качество продукции по рынку в целом будет падать.
– У многих компаний есть аудит поставщиков. Этот механизм работает?
– Мы проходили аудит в нескольких крупнейших компаниях, у всех получили высшие оценки. Но часто по факту, когда мы приходим на конкурс, оказывается, что все эти проверки имеют далеко не первостепенное значение. При этом сами аудиторы разводят руками. Они все понимают разницу между производителем, который имеет собственный научный центр, длительную историю, высокий уровень доверия, высокий уровень качества и высокий уровень ответственности, и обыкновенным перекупщиком. Или небольшим цехом, который производит ЛКМ, но по большому счету, один-два брака могут эту компанию разорить.
Для исправления ситуации заказчику нужно повышать значимость аудита как критерия оценки. Сейчас, условно говоря, есть 100 баллов. 80-90 баллов дается за цену, 10 баллов – на аудит. Соотношение должно быть другое – как минимум, 50/50. Если мы говорим о серьезных сложных материалах, то не следует ориентироваться исключительно на цену.
Многие компании очень серьезно подходят к аудиту. Приезжают по 6-10 человек, которые инспектируют качество работы снабжения, качество ОТК на приемке и выпуске продукции. Идет проверка научного центра, сырья, работы складов, естественно, производства. После того как заказчик так "прошерстил" предприятие, он четко понимает, что компания может сделать, а что нет. Если заказчик настроен досконально о поставщике все узнать, мы в этой части открыты. Поэтому, конечно, аудит должен играть намного большее значение при выборе поставщика.
– Какие компании предлагают своим поставщикам пройти такой аудит и сколько он длится?
– Аудит длится около недели. Что касается морских покрытий, например, у нас проходил аудит "Объединенной судостроительной корпорации" (ОСК), по итогам которого нам выдали один из высших баллов. Из других секторов – "Объединенная авиационная корпорация" (ОАК), "Яковлев". "Газпром", скорее всего, тоже такие аудиты проводит.
В декоративном сегменте тот же "Леруа Мерлен" проводил аудиты всех поставщиков, и у них это гораздо больше влияло при проведении тендеров.
– Но это частная компания, возможностей у нее гораздо больше...
– Если ссылаться только на то, что государственным компаниям сложно провести аудит, то зачем он нужен? Если вы можете только сравнить два предложения по цене и выбрать более выгодное, то хотя бы пользуйтесь ГОСТами, хотя бы по требованиям к толщине покрытий. Даже этого нет. И в этот момент государственная компания включает коммерческую жилку и ищет, где подешевле. Часто приходится сталкиваться с тем, что снабженцы боятся выбирать материалы по качеству выше, но дороже. При этом они говорят, мы не сможем оправдаться, почему мы взяли дороже, нам лучше взять дешевле, к нам вопросов вообще никаких не будет.
– Частный заказчик может вмешаться и сам выбрать ЛКМ?
– С заказчиком этот вопрос решить можно. Но если мы говорим о строительстве судна, к примеру, сухогруз проекта RSD59 стоит порядка 1,2-1,5 млрд рублей. Краски там максимум на сумму около 40 млн рублей. Как правило заказчику не хочется этим заниматься. Хотя есть заказчики, которые относятся к этому очень серьезно. С ними нам проще разговаривать. Они параллельным импортом тащат иностранцев, они проводят тестирования и подробно обсуждают с нами эту тему. Но таких немного.
– Например?
– Тот же рыбопромысловый холдинг "Норебо". Они очень внимательно относятся к своим материалам. "Окская судоверфь" тоже очень серьезно следит за своими материалами. Хотя верфь является не конечным заказчиком, а производителем работ, для нее уровень качества более важен, чем сделать подешевле.
Огромный плюс "Окской судоверфи" или одной из лучших верфей ОСК, с точки зрения экономики и скорости строительства, – завода "Красное Сормово" заключается в строительстве больших серий. При этом почему-то длинных серий в России практически нет. А экономика в судостроении достигается где-то на третьем-четвертом судне в серии. Если вы хотите хоть немного заработать, вам нужно хотя бы пятое построить.
Если вы не закладываете серию, вы всегда будете убыточны. Я сам работал в судостроении. До спуска на воду первого судна весь проект практически полностью переделывается. Это нереально все рассчитать. Может, на третьем-четвертом судне ты получишь документацию, по которой построишь без переделок. Это при том, что у тебя специалисты сохранятся и поставщики.
В моем понимании, как раз к серийности нашему судостроению и стоит стремиться.
– Помимо слабой серийности, с точки зрения производителя материалов, еще есть какие-то общие для отрасли проблемы?
– Есть серьезная проблема с технологией нанесения и соблюдением климатических условий. Мы живем в большинстве на Севере, и очень часто у нас нарушаются условия для нанесения материалов. У нас влажность повышенная, температура пониженная. Плюс, на некоторых судоремонтных предприятиях страдает культура производства. Соответственно, для нас задача заключается в том, чтобы сохранить антикоррозионный уровень материалов, но при этом дать возможность малярам красить в нарушение "климатики". Поэтому мы делаем материалы с некоторым запасом, чтобы исполнители работ, даже нарушив климатические условия, все равно получили нужный результат.
Так, у нас есть материалы, которые можно наносить и в минус 20. Есть материалы, которые можно наносить при повышенной влажности. В том же Мурманске или Архангельске идеальное климатическое состояние очень редко встречается. Для этих регионов у нас есть варианты решения проблемы.
Главное, чтобы заказчик адекватно оценивал те условия, в которых он будет наносить. Иногда покупают, рассчитывая красить летом, в итоге красят зимой, а потом задают вопросы, почему так получилось. Нам нужно четкое задание. Если хочешь красить летом, это одни материалы. Если хочешь красить зимой в снег и дождь – это немного другие материалы. Мы решим проблему, это вопрос не денег, нам просто надо понимать, в каких условиях будут красить.
Есть такие заказчики, часто это госкомпании, которые проводят конкурсы летом и рассчитывают красить в начале осени, а по факту работают зимой. Мы добавляем 3-4 месяца и даем зимний материал. Додумываем за клиента, но проблему решаем.
Беседовал Александр Полунин
Фото: "Русские краски"
Erid: 2VtzqvvGgnu
– Александр Олегович, какие новые ЛКМ для морской индустрии сегодня разрабатывают "Русские краски"?
– Работы по новым материалам наша компания ведет постоянно. На рынке судостроения и судоремонта мы присутствуем уже почти 8 лет и практически каждый год выпускаем новые морские лакокрасочные покрытия. Сейчас мы проводим полную сертификацию материалов с новыми эпоксидами, будем выводить новое ледовое покрытие первого класса уровня ведущих зарубежных производителей, разработали и готовим к выводу на рынок новый грунт, адаптированный для удобства пользователей.
Еще один интересный и сложный продукт, который в настоящее время проходит сертификацию, – покрытие для топливных цистерн. Материалов такого уровня раньше в России не было. До этого использовались только классические материалы 1970-х годов разработки. Сложность такого материала заключается в минимизации воздействия на топливо, которое хранится в цистерне. Разработка такого материала – достаточно сложный процесс с очень дорогостоящими испытаниями.
Кроме того, недавно сертифицировали покрытие для питьевых цистерн. Это не менее сложный продукт. В "питьевке" мы должны одновременно соединить гигиенические нормы, которые подразумевают отсутствие вреда для здоровья людей, и очень жесткие требования по антикоррозионной защите. Это прямо противоречащие друг другу показатели, мы их «скручивали» года три. Это была сложная работа, но мы ее провели. В итоге материал сделан и прошел всю сертификацию.
Потребность в таких материалах появилась после ухода с рынка иностранцев. Несмотря на то, что объем рынка таких покрытий очень маленький, спрос на них есть. Наша цель – полностью окрасить судно или корабль, для этого нам надо закрывать и эти вопросы.
Сложность здесь заключается в том, что все поверхности находятся в разных климатических и антикоррозионных условиях, подвергаются разным воздействиям: топливо, вода, лед, обрастания, атмосфера, солнце, кислоты. Это очень разные условия эксплуатации. Поэтому для нас было важно полностью закрыть всю линейку морских лакокрасочных покрытий одной маркой.
– Это удалось?
– По факту, уже да. Вся линейка лакокрасочных покрытий закончена, осталось завершить некоторые сертификационные процедуры.
– В ходе нашего общения в прошлом году вы оценивали долю рынка компании примерно в 10%. Ситуация изменилась?
– Практически нет. Новая сложность в том, что мы не всегда понимаем, что с рынком сейчас происходит по факту. Объективных данных, от которых можно было бы оттолкнуться, нет. Если до 2022 года все данные были открыты, все производители известны, а все объемы понятны и прозрачны, то после после ухода иностранцев мы не можем точно просчитать, что с рынком происходит. По нашим ощущениям, он сократился, объемы строительства притормаживаются.
В то же время рынок очень инерционный и останавливается медленно. Если проект запущен, то его пытаются довести до конца. Но сдачи точно сдерживаются, потому что у нас есть примеры верфей, которые практически всё достроили, спустили на воду, но при этом сдать не могут из-за того, что отсутствует несколько агрегатов, которые не могут быть поставлены по понятным причинам. Верфи не могут получить деньги, соответственно, не могут получить новые проекты. Эта ситуация точно есть, но в каком масштабе, у нас нет точных данных.
Среди других факторов – практически неконтролируемый приход на рынок множества небольших производителей. Мы не очень понимаем, что с китайцами, которые заходят на наш рынок, какую долю они забирают. Не видим, сколько завозится параллельным импортом, потому что это закрытые схемы, которые не отражаются в отчетности.
Плюс реформирование и реорганизация в ряде корпораций ведет к тому, что некоторые проекты приостанавливаются. Это тоже сказывается на рынке. Поэтому мы свою долю так же примерно оцениваем в 10%, но мы стали хуже чувствовать цифры.
– Поговорим о специфике продукции для разных сегментов. В последние годы набирают популярность электросуда. У "Русских красок" есть продукция для таких судов?
– Да. Например, наша продукция используется на верфи электрического судостроения "Эмпериум", куда мы поставляем шпаклевку. Недавно в Ярославле был спущен на воду полностью нами покрашенный электрокатамаран "Белояр", построенный на верфи "Паритет-Центр".
Особенность электросудов в том, что там используется алюминий, а у нас есть яхтенная линейка, созданная с учетом опыта работы с авиацией. Когда мы начинали на судостроительном рынке, у нас был большой плюс – авиационные материалы, и мы могли использовать этот опыт. Там же тоже используется алюминий, поэтому мы смогли создать линейку яхтенных материалов, которой нет у других российских производителей. По сравнению с морскими яхтенные покрытия имеют совсем другой вид, там другой глянец.
Эту линейку как раз использовала верфь "Паритет" для окраски катеров проекта "Лукер" и небольших яхт, а затем и для большого электрокатамарана. Поэтому с учетом того, что у нас есть опыт работы с яхтенной краской и алюминием, для нас переход на "электрички" не создает никаких проблем. Мы спокойно можем это делать.
– В чем особенность яхтенного сегмента?
– Здесь меньше борьбы с коррозией, важнее внешний вид. Эти покрытия ближе к авиационным покрытиям, где очень высокие требования. Ведь самолеты под солнцем находятся большую часть времени, а влияние ультрафиолета в воздухе намного жестче, чем у любого объекта на земле. Плюс еще жесткость в перепадах температуры. Если у нас погода меняется плюс-минус пять градусов в течение дня и постепенно, то здесь перепад от минус 40 до плюс 40 градусов происходит в течение часа. Для краски это очень серьезная нагрузка.
Имея в руках разработанные материалы для авиационной отрасли, нам легко было перейти и сделать материалы для яхтенного сегмента.
– В последние годы также развивается композитное судостроение. С композитами вы работаете?
– На композиты материалы идут те же самые материалы, только толщина грунтовок другая. В данном случае материалы несут больше связывающую функцию между эмалью и самим композитом. Если в стальном судостроении идет в основном антикоррозионная работа, то здесь опять же ближе к декоративным материалам.
– А что касается ЛКМ для грузовых судов, например, сухогрузов?
– С ними проще. Все основные материалы уже давно разработаны. Сейчас мы просто их продолжаем улучшать.
– Вы упомянули разрабатываемый материал для ледокольного флота. С этим сегментом вы уже работаете?
– Мы начали работать, но сейчас стоит большой вопрос, что делать дальше с ледокольным флотом. Нам неожиданно предъявили требования, что все заказчики хотят первый класс, но вопрос в цене. Ледокольное покрытие уровня Inerta 160 или Marathon IQ в Европе и Китае стоит около 3 тыс. рублей за литр. В России подобные покрытия некоторые производители предлагают за 1,5 тыс. рублей. Мы в некотором недоумении по этому поводу, потому что все знают, сколько стоят компоненты для таких покрытий. Например, там используются исключительно отвердители от одного конкретного западного производителя сырья.
Часто задают вопрос, почему для лакокрасочных материалов используются импортные компоненты, ведь в основе – та же нефть. Проблема в том, что между нами и "нефтянкой" стоит целая отрасль – химическая. Мы стоим четвертым-пятым уровнем и не можем взять продукты нефтепереработки и из них сделать краску. Нам еще нужна целая отрасль, на которую никто не обращал внимание, и она практически полностью в России теперь отсутствует. Поэтому большая часть химии – импорт.
В целом лакокрасочная отрасль очень глобальна. В мире нет страны, в которой от "нефтянки" до краски все делается внутри. Поэтому цены глобальные, все их прекрасно знают. Плюс-минус 10-20% играют, но вариант, что материал, который стоит три тысячи, а продается за полторы, для нас пока остается загадкой.
Мы со своей стороны делаем покрытие уровня Inerta. Мы понимаем, что оно будет точно немного дешевле, чем европейские аналоги, но на их уровне. Дальше будем действовать исходя из того, что рынок захочет. Если рынок продолжит брать дешевые материалы и делать ставку на цену, значит будет материал, который хочет рынок. Только потом будет обидно, когда начнут говорить, как это было раньше, что в России производят не очень хорошее качество, а вот у европейцев было "совсем другое".
– Сколько по времени занимает разработка новых материалов?
– В среднем на разработку одного материала в нашем научно-исследовательском центре уходит от одного года до трех лет. Далее встает вопрос сертификации. После того, как мы проходим собственные внутренние испытания, у нас еще есть испытания для ВМФ и гражданских заказчиков. Там испытания длятся до полутора лет. Если все хорошо, то полный цикл занимает до 4-5 лет. Если мы говорим о серьезных материалах, то это примерно такие сроки. Соответственно, и глубина планирования для таких ЛКМ у нас должна быть достаточно длинной.
Есть, конечно, покрытия, которые делаются быстрее. Как раз так получается с подводным бортом.
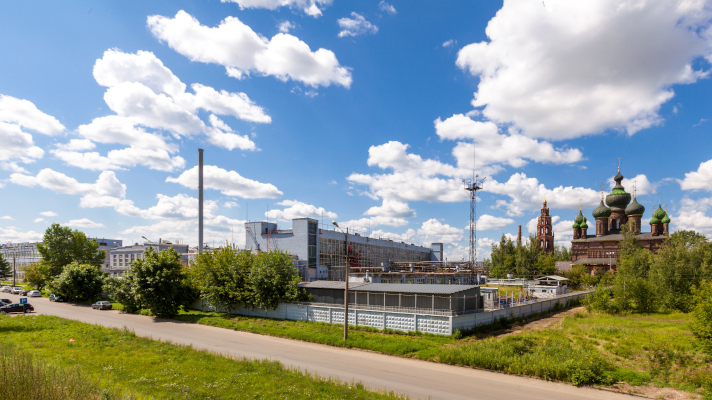
Завод "Русские краски" в Ярославле
– На какой срок службы рассчитаны материалы "Русских красок"?
– В последнее время для некоторых материалов мы продлили срок службы до 15 лет, даже для подводного грунта. До этого мы все испытания проводили на срок до 5 лет. Увеличение в 3 раза связано с высокими требованиями государственных заказчиков к морским покрытиям. Этот же грунт используем и на гражданские суда, поэтому там сроки службы тоже увеличились.
Хотя это отдельная большая тема – сроки службы, которые нужны клиенту. Мы на протяжении всего времени работы смотрели на международные компании. Российский рынок морских покрытий, в отличие от индустриального рынка, на 80% занимали иностранцы. Этот рынок был не элитным, но с точки зрения качества материалов очень высоким. Когда мы заходили на рынок, к нам были требования выпускать материалы не ниже мировых стандартов. Мы на это изначально были нацелены. И завод может себе это позволить, и научно-исследовательский центр у нас очень большой. В результате мы довели уровень материалов до мирового, а по некоторым позициям даже выше, чем у иностранцев.
Но после ухода иностранцев рынок поменялся, в моем понимании, в худшую сторону. У нас сейчас в этом году первым и главным показателем на 90% стала цена. В целом рынок стал очень резко падать по качеству. Стали заходить неспециализированные производители, которые думали, что иностранцы ушли, соответственно, место освободилось. С индустриального рынка стало много компаний заходить. Интересно, что на мировом рынке происходит наоборот: там изначально создаются продукты для сложного рынка морских покрытий, затем эти продукты упрощаются до индустриального рынка, а далее – до рынка декоративных материалов. В России мы зачастую наблюдаем противоположную тенденцию.
В результате этих процессов стали резко падать требования к материалам. И это на самом деле колоссальная проблема, потому что для нас это некоторое переформатирование. Мы, конечно, перестроимся, но в целом то, что требования к материалам снизились, это очень печально.
– Кто снижает требования, заказчик судна?
– Зачастую, да. При этом сам же заказчик часто жалуется, что он хотел бы получать материалы все того же уровня, но вынужден в связи с законодательством и, иногда, в связи с формальным подходом некоторых подразделений, выбирать исключительно по цене.
В итоге заказчик получает материалы, которые служат 2-3 года – срок гарантии. Что с ними будет потом происходить, никто не представляет, да и никто сильно не беспокоится по этому поводу. Это на самом деле огромная проблема для всех производителей, которые работают на этом рынке. Последние лет пять мы все занимались качеством. Мы разгоняли материалы до уровня мировых производителей, но происходящее сейчас всю эту систему рушит.
– Как приоритет цены при закупках сочетается с разработкой перспективных материалов?
– Это очень плохо для науки, которая занималась разработкой этих материалов. В целом качество отечественных материалов начинает падать. С такой ситуацией мы вернемся к тому, что было лет 15 назад.
Что с этим делать, никто пока не знает. Единственный вариант, который у нас есть – выпускать разные линейки. Для тех клиентов, которым важна долговечность антикоррозионных материалов, мы делаем одну линейку. Для тех, кто просто смотрит на цену, делается вторая линейка.
– Что могло бы изменить эту ситуацию?
– Вопрос к заказчикам, чего они хотят. Что важнее, влезть в бюджет, и чтобы те подразделения, которые отвечают за закупки, получили KPI за снижение цены, или получить материалы высокого уровня. Большинство заказчиков выбирают вариант попроще, подешевле, глубоко не вникая. Специалистов, которые в этой теме понимают, становится все меньше и меньше.
В крупных корпорациях еще есть такая проблема. У них нет человека, который будет с кораблем работать 5-10 лет, там происходит постоянная ротация через 1-3 года. Соответственно, у них нет длинной ответственности. В итоге, если все это будет продолжаться, мы получим то, что качество продукции по рынку в целом будет падать.
– У многих компаний есть аудит поставщиков. Этот механизм работает?
– Мы проходили аудит в нескольких крупнейших компаниях, у всех получили высшие оценки. Но часто по факту, когда мы приходим на конкурс, оказывается, что все эти проверки имеют далеко не первостепенное значение. При этом сами аудиторы разводят руками. Они все понимают разницу между производителем, который имеет собственный научный центр, длительную историю, высокий уровень доверия, высокий уровень качества и высокий уровень ответственности, и обыкновенным перекупщиком. Или небольшим цехом, который производит ЛКМ, но по большому счету, один-два брака могут эту компанию разорить.
Для исправления ситуации заказчику нужно повышать значимость аудита как критерия оценки. Сейчас, условно говоря, есть 100 баллов. 80-90 баллов дается за цену, 10 баллов – на аудит. Соотношение должно быть другое – как минимум, 50/50. Если мы говорим о серьезных сложных материалах, то не следует ориентироваться исключительно на цену.
Многие компании очень серьезно подходят к аудиту. Приезжают по 6-10 человек, которые инспектируют качество работы снабжения, качество ОТК на приемке и выпуске продукции. Идет проверка научного центра, сырья, работы складов, естественно, производства. После того как заказчик так "прошерстил" предприятие, он четко понимает, что компания может сделать, а что нет. Если заказчик настроен досконально о поставщике все узнать, мы в этой части открыты. Поэтому, конечно, аудит должен играть намного большее значение при выборе поставщика.
– Какие компании предлагают своим поставщикам пройти такой аудит и сколько он длится?
– Аудит длится около недели. Что касается морских покрытий, например, у нас проходил аудит "Объединенной судостроительной корпорации" (ОСК), по итогам которого нам выдали один из высших баллов. Из других секторов – "Объединенная авиационная корпорация" (ОАК), "Яковлев". "Газпром", скорее всего, тоже такие аудиты проводит.
В декоративном сегменте тот же "Леруа Мерлен" проводил аудиты всех поставщиков, и у них это гораздо больше влияло при проведении тендеров.
– Но это частная компания, возможностей у нее гораздо больше...
– Если ссылаться только на то, что государственным компаниям сложно провести аудит, то зачем он нужен? Если вы можете только сравнить два предложения по цене и выбрать более выгодное, то хотя бы пользуйтесь ГОСТами, хотя бы по требованиям к толщине покрытий. Даже этого нет. И в этот момент государственная компания включает коммерческую жилку и ищет, где подешевле. Часто приходится сталкиваться с тем, что снабженцы боятся выбирать материалы по качеству выше, но дороже. При этом они говорят, мы не сможем оправдаться, почему мы взяли дороже, нам лучше взять дешевле, к нам вопросов вообще никаких не будет.
– Частный заказчик может вмешаться и сам выбрать ЛКМ?
– С заказчиком этот вопрос решить можно. Но если мы говорим о строительстве судна, к примеру, сухогруз проекта RSD59 стоит порядка 1,2-1,5 млрд рублей. Краски там максимум на сумму около 40 млн рублей. Как правило заказчику не хочется этим заниматься. Хотя есть заказчики, которые относятся к этому очень серьезно. С ними нам проще разговаривать. Они параллельным импортом тащат иностранцев, они проводят тестирования и подробно обсуждают с нами эту тему. Но таких немного.
– Например?
– Тот же рыбопромысловый холдинг "Норебо". Они очень внимательно относятся к своим материалам. "Окская судоверфь" тоже очень серьезно следит за своими материалами. Хотя верфь является не конечным заказчиком, а производителем работ, для нее уровень качества более важен, чем сделать подешевле.
Огромный плюс "Окской судоверфи" или одной из лучших верфей ОСК, с точки зрения экономики и скорости строительства, – завода "Красное Сормово" заключается в строительстве больших серий. При этом почему-то длинных серий в России практически нет. А экономика в судостроении достигается где-то на третьем-четвертом судне в серии. Если вы хотите хоть немного заработать, вам нужно хотя бы пятое построить.
Если вы не закладываете серию, вы всегда будете убыточны. Я сам работал в судостроении. До спуска на воду первого судна весь проект практически полностью переделывается. Это нереально все рассчитать. Может, на третьем-четвертом судне ты получишь документацию, по которой построишь без переделок. Это при том, что у тебя специалисты сохранятся и поставщики.
В моем понимании, как раз к серийности нашему судостроению и стоит стремиться.
– Помимо слабой серийности, с точки зрения производителя материалов, еще есть какие-то общие для отрасли проблемы?
– Есть серьезная проблема с технологией нанесения и соблюдением климатических условий. Мы живем в большинстве на Севере, и очень часто у нас нарушаются условия для нанесения материалов. У нас влажность повышенная, температура пониженная. Плюс, на некоторых судоремонтных предприятиях страдает культура производства. Соответственно, для нас задача заключается в том, чтобы сохранить антикоррозионный уровень материалов, но при этом дать возможность малярам красить в нарушение "климатики". Поэтому мы делаем материалы с некоторым запасом, чтобы исполнители работ, даже нарушив климатические условия, все равно получили нужный результат.
Так, у нас есть материалы, которые можно наносить и в минус 20. Есть материалы, которые можно наносить при повышенной влажности. В том же Мурманске или Архангельске идеальное климатическое состояние очень редко встречается. Для этих регионов у нас есть варианты решения проблемы.
Главное, чтобы заказчик адекватно оценивал те условия, в которых он будет наносить. Иногда покупают, рассчитывая красить летом, в итоге красят зимой, а потом задают вопросы, почему так получилось. Нам нужно четкое задание. Если хочешь красить летом, это одни материалы. Если хочешь красить зимой в снег и дождь – это немного другие материалы. Мы решим проблему, это вопрос не денег, нам просто надо понимать, в каких условиях будут красить.
Есть такие заказчики, часто это госкомпании, которые проводят конкурсы летом и рассчитывают красить в начале осени, а по факту работают зимой. Мы добавляем 3-4 месяца и даем зимний материал. Додумываем за клиента, но проблему решаем.
Беседовал Александр Полунин
Фото: "Русские краски"
Erid: 2VtzqvvGgnu
Другие новости компании «АО "Русские краски"»
Самые читаемые
Российское судостроение в марте 2025 года
9 Апреля 2025
ОСК предлагает построить замену научному судну "Михаил Сомов" на Адмиралтейских верфях
10 Апреля 2025
ОСК разрабатывает проекты танкеров-газовозов для компаний "Газпрома"
14 Апреля 2025
Лесник, перевернувший судостроение: кто же изобрел гребной винт?
12 Апреля 2025
НОВЫЕ КОМПАНИИ